Citadelle des savoir-faire de Bruay-sur-l’Escaut
L’impression 3D se veut toujours plus fiable
Le 10 septembre, les entreprises et le secteur de la recherche se sont retrouvés à la Citadelle des savoir-faire à Bruay-sur-l’Escaut pour échanger autour de l’impression 3D.
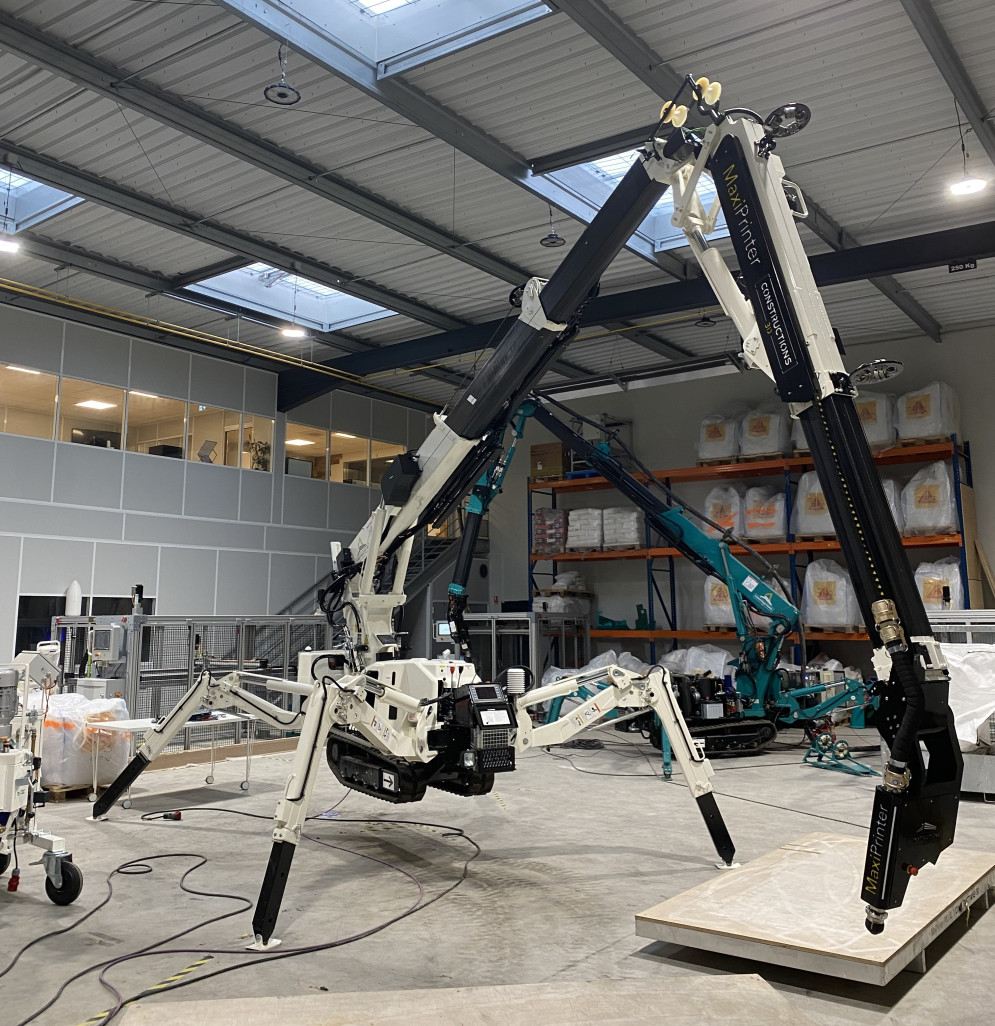
Ingénieurs, chefs de projets et entrepreneurs se sont réunis ce 10 septembre à Bruay-sur-l’Escaut, au cœur de la Citadelle des savoir-faire, le centre de découverte scientifique autour de l’impression 3D et du scan 3D. Durant cette journée, EuraMaterials et le Club impression 3D ont organisé la deuxième session de travail de la communauté Sustain-3D. En effet, cette technologie s’impose sur le marché de l’industrie grâce à sa capacité de fabrication de pièces complexes. Elle impacte tous les secteurs d’activité, de la construction à la santé et la défense.
Construction et mobilité
À l’image de l’entreprise nordiste Constructions-3D, basée à la Citadelle, qui se distingue par son expertise dans le BTP. Alors qu’il faut compter cinq heures pour que le béton classique sèche, celui de l’entreprise nordiste n’a besoin que de quelques secondes. «Avec une imprimante 3D béton qui va construire une maison par jour…on peut déjà juguler la croissance du mal-logement» indique Antoine Motte, cofondateur de Constructions-3D. Les imprimantes MaxiPrinter fabriquées par l’entreprise ont d’ailleurs été utilisées pour construire les 2 800 m² de la Citadelle.
De son côté, Farm-3D développe des ateliers mobiles numériques 4.0. Ces « containers » aménagés sont de véritables micro-usines de fabrication additive, offrant une solution face au manque d’infrastructures dans des régions isolées. Christophe Raillon, fondateur de la start-up nordiste lancée en 2023, souligne la nécessité de déployer cette innovation dans le secteur de l’humanitaire et de la défense. Des pièces détachées imprimées en 3D ont ainsi été développées. Farm-3D a imaginé des micro-usine de fabrication additive industrielle 4.0, de pièces de rechange et de composants techniques projetables en environnements isolés et extrêmes, au service du maintien en conditions opérationnelles d'activités critiques.
Contrôle et traçabilité
Mais face à ces utilisations pointues, les techniques de monitoring et de contrôle lors des process de fabrication se doivent d’être toujours plus efficaces et fiables. Ainsi, le contrôle in situ regroupe des techniques permettant de fabriquer des pièces de façon reproductive et de détecter les dérives du procédé. Pour ce faire, par exemple, le lit de poudre et le bain de fusion sont équipés de caméras thermiques et coaxiales afin de monitorer l’énergie déposée. «Ces techniques ne sont cependant pas applicables à grande échelle» explique Olivier Dellea, directeur de recherche au centre CEA.
La méthode de détection des défauts par contrôle acoustique offre alors une précision supérieure grâce à des capteurs reliés à un logiciel. «Ils sont placés sous le plateau pour localiser la couche de dépôt du filament» illustre Fan Zhang, experte CND chez Cétim. Certains logiciels de pointe sont également utilisés pour assurer la traçabilité des process. C’est le cas de Dmeos, un outil de pilotage développé et utilisé par Farm-3D et visant à répondre aux exigences ISO.
Si l’avenir de l’impression 3D passe des process hautement fiables, il repose également sur la capacité des entreprises à réduire leur empreinte carbone. Un enjeu de taille pour le secteur du bâtiment. Dans cette optique, le lin est de plus en plus utilisé. «La paille de lin divise les émissions par trois» souligne Antoine Motte, qui a utilisé ce matériau sur le chantier de la tour de la Citadelle des savoir-faire, démarré en 2022. Les murs imprimés ont ainsi été remplis de paille de lin cultivée localement. Un bel exemple de production durable.
Pour Aletheia Press, Aurore Duclaye